A Bourdon tube is the working mechanism of analogue pressure measurement devices and is based on the principle of elasticity.
While sophisticated measuring tools employ LCD screens to display measurement figures accurately up to several decimal places, the humble analogue gauge remains defiantly present in almost all pressure measurement devices. Here, we attempt to understand the working of this essential device.
Recommended Video for you:
What Is A Bourdon Tube?
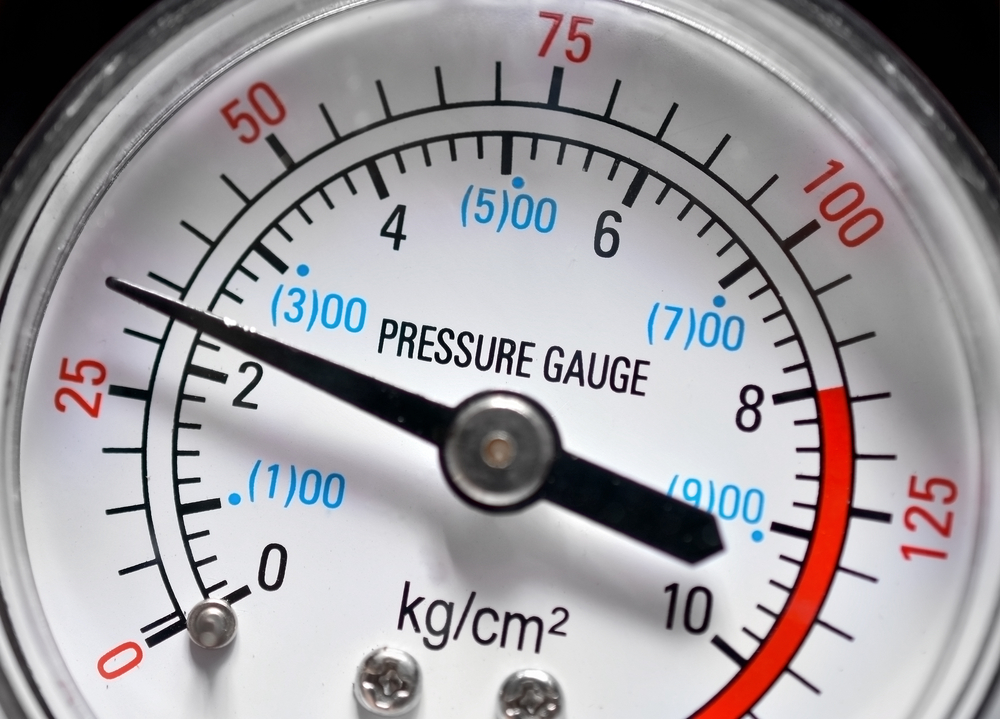
A Bourdon tube is the working mechanism for any analogue pressure measurement device. It is named after its inventor, Eugene Bourdon, who created and patented the design. The phenomenon of elasticity on which it is based provides reasonably accurate results, even in the present day and age, despite very little advancements in the underlying technology.
It comprises an elastic tube that flexes when subjected to pressure. This movement is harnessed by connecting the tube to a gearing mechanism that in turn connects to a pointer on a scale/gauge.
How Does A Bourdon Tube Work?
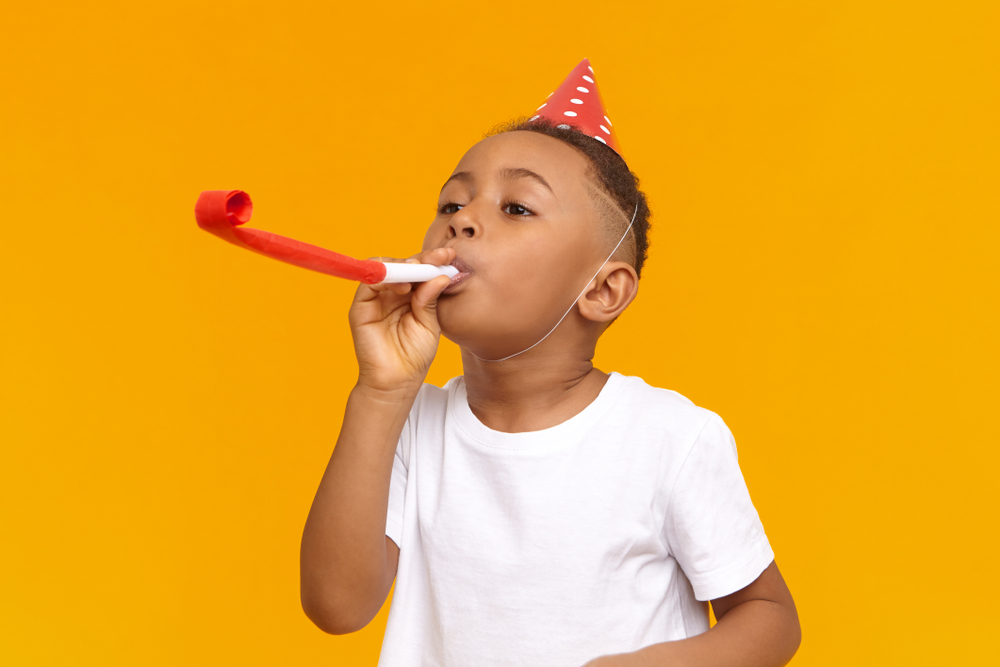
A party horn is the best illustration of the working of a Bourdon tube. As one blows into the mouthpiece, the air forces the flattened coil of paper/plastic to unfurl, creating a loud sound in the process. The amount of uncoiling and the intensity of the sound generated is directly proportional to the force applied at the mouthpiece.
<span data-mce-type=”bookmark” style=”display: inline-block; width: 0px; overflow: hidden; line-height: 0;” class=”mce_SELRES_start”><span data-mce-type=”bookmark” style=”display: inline-block; width: 0px; overflow: hidden; line-height: 0;” class=”mce_SELRES_start”></span></span>
Working of Bourdon gauge tube
A bourdon tube is very similar to a party horn in its working. When pressure is applied at the inlet, the flattened tube inflates, resulting in an increase in its cross-sectional area. The coil now straightens out, uncoiling in proportion to the amount of pressure being applied.
This movement can be leveraged for measuring pressure or other associated parameters by attaching a pointer and a dial at the coiled end of the tube.
Construction Of A Bourdon Tube Gauge
A Bourdon tube can be made from many materials, but it is essential for them to have spring-tempering properties. Spring tempering strengthens the metal while enhancing elastic properties, thereby making repeated coiling and uncoiling possible.
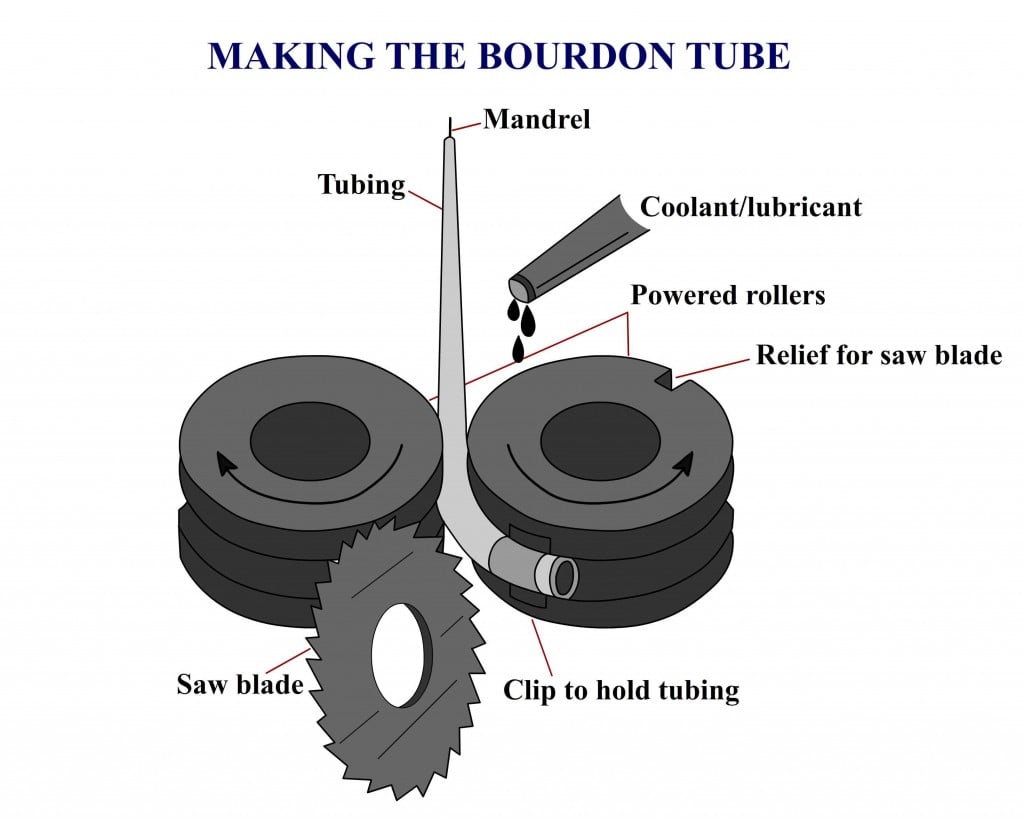
The tube is made by drilling a round or elliptical cross-section into a stock of the desired material. It is then passed through a series of rollers that bend it into the required shape and flatten it to coil it. The hollow created by drilling expands and contracts based on the movement of the working fluid, resulting in coiling and uncoiling of the Bourdon tube.
Some commonly used materials include steel alloys, beryllium copper and phosphor bronze. The inlet pressure can be exerted by any medium, including air, water and oil. While stainless steel is suitable for heavy oils, beryllium copper is suited for extremely high-pressure applications and phosphor bronze is used for general applications that employ air, water and even some light oils.
Types Of Bourdon Tubes
1. C-type
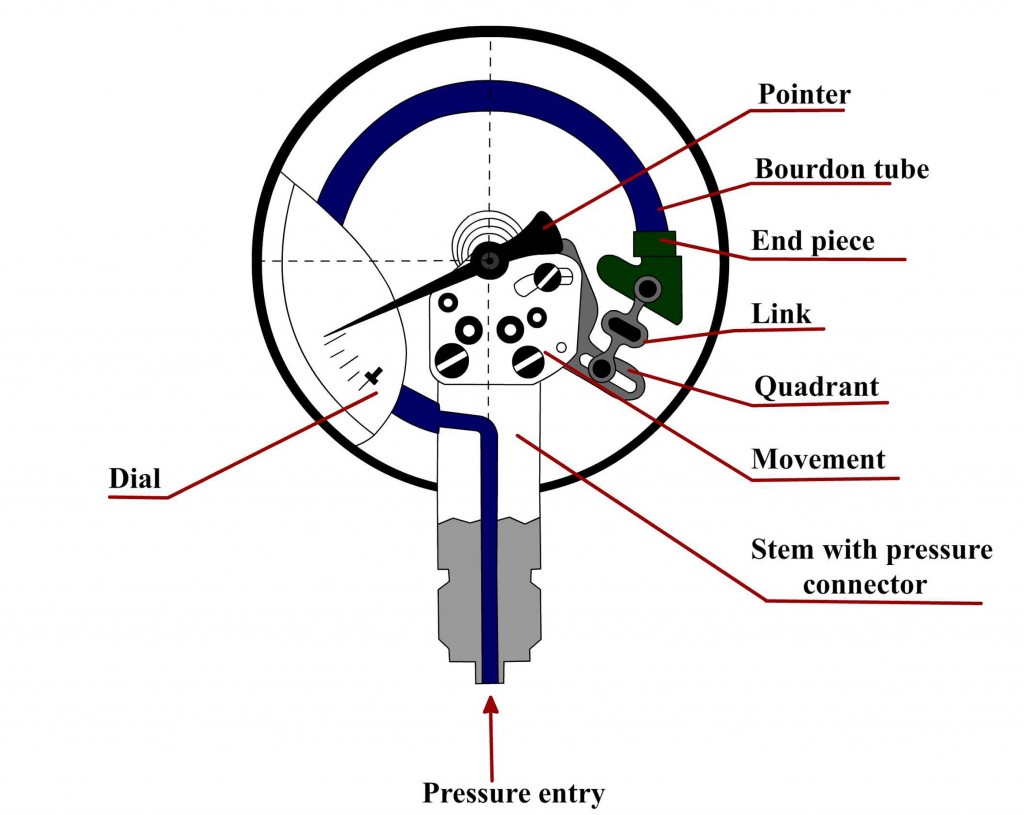
This is the most commonly found tube. It can withstand pressures of up to 10,000 kilopascals. It consists of a tube bent into a C shape and is used for low-pressure applications.
2. Spiral Type
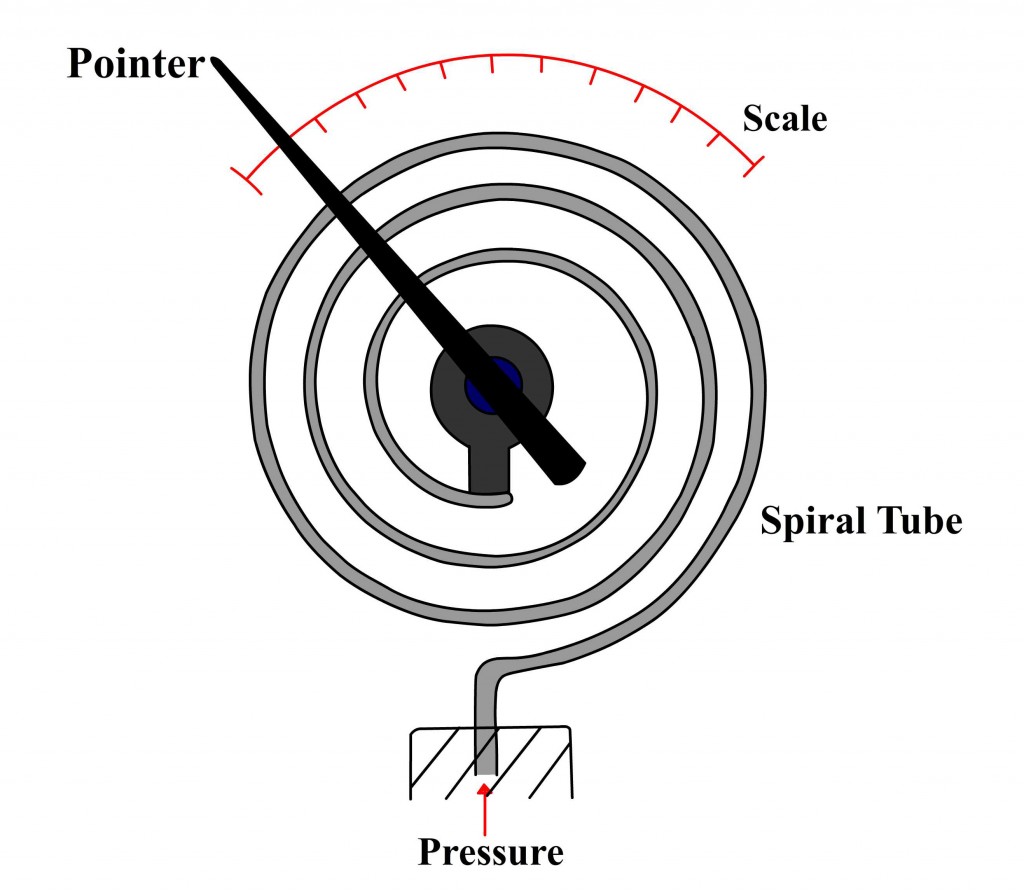
This type of Bourdon tube is spiral in shape and suitable for pressures up to 28,000 kilopascals.
3. Helical Type
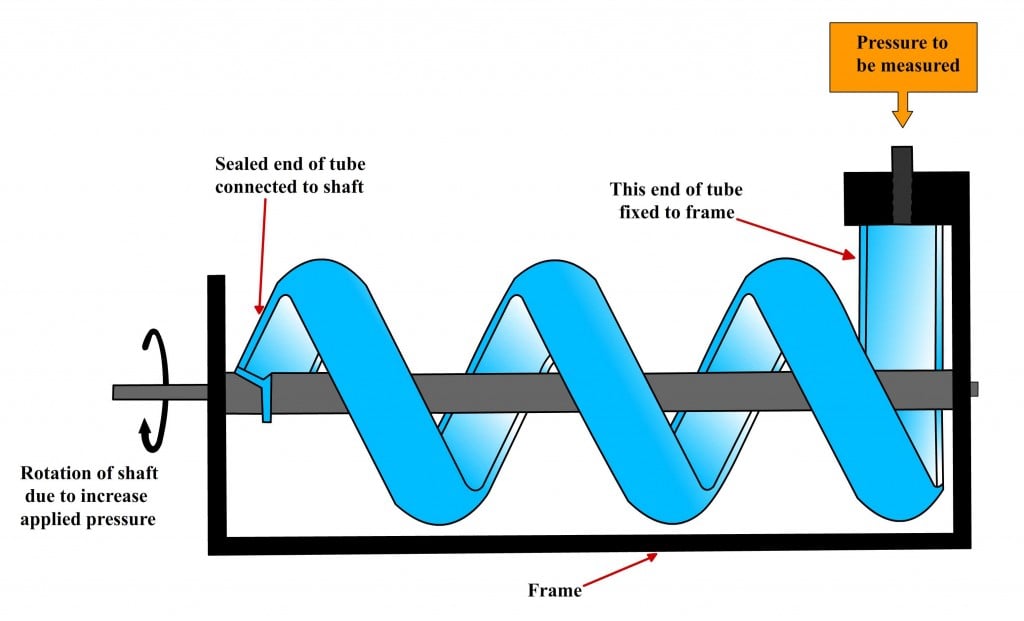
This type of Bourdon tube is helical in shape and suitable for pressures of up to 500,000 kilopascals.
While C-type Bourdon tubes are inexpensive to manufacture and easier to find, their pressure sensitivity is limited. Spiral and helical tubes are therefore used for high-pressure applications or those where more precision is required.
Advantages And Disadvantages Of Bourdon Tubes
Bourdon tubes have many advantages, which result in their wide employment:
1. They give reasonably accurate results.
2. They are simple in construction and inexpensive to produce.
3. They can be safely used for the accurate measurement of high pressures.
4. They can be modified to generate electrical outputs.
5. Bourdon tube gauges have high repeatability, i.e., they can accurately record the same pressures multiple times.
Despite being almost omnipresent in pressure measurement devices, Bourdon tubes have certain inherent disadvantages:
1. A Bourdon tube responds slowly to changes in pressure.
2. An amplification mechanism is needed to generate readings, as the movement of the free end of the Bourdon tube is quite low.
3. While Bourdon tube gauges can produce accurate results, they cannot be used for precision applications.
4. Bourdon tubes suffer from hysteresis, a condition that causes the tube to retract slower when moving from a high scale reading to a low scale reading. This results in the scale showing a slightly “higher than actual” reading.
5. Bourdon tubes are medium-sensitive, i.e., they are usually calibrated to only work with a particular medium. Using another medium can affect the reading owing to its own density and weight, and thus result in an error. This must be accounted for before changing the medium.
Application And Future Scope Of Bourdon Tubes
Any type of Bourdon tube can measure pressure proportional to the arc it subtends, i.e., the more curved the arc, the greater is the pressure sensitivity of the device. Thus, spiral and helical tubes are more sensitive to pressure changes than a C-type tube. This, however, increases the complexity, and consequently, the cost of manufacturing.
Here is a list of applications that employ the Bourdon tube gauge:
1. Direct pressure measurement – Measuring the absolute pressure of any system.
2. Differential pressure measurement – Measuring the difference in pressure of two pressurized systems.
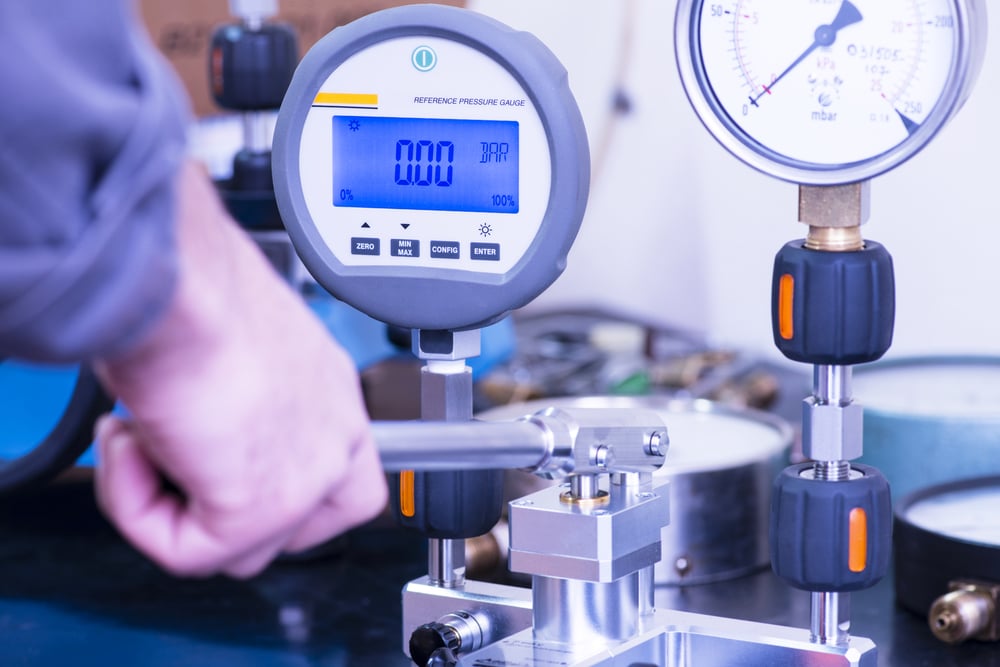
With the improvement in semiconductor technology, Bourdon tubes are either dependent on or being completely replaced by electronic systems that can be used in high-risk environments.
However, Bourdon tube gauges will continue to dominate the pressure measurement industry until their electronic counterparts become economically viable for a wider range of applications.