Alloys can be reversed into their base metals using a variety of techniques, but it may not always be profitable to do so.
Alloys are amongst the most significant advancements in metallurgy. They bring forth the best characteristics of their constituent metals, greatly increasing their avenues of application.
An important feature of alloys is that they are homogenous mixtures, rather than chemical compounds. Mixtures are characterized by their ability to be decomposed into their constituting elements. Does the same hold true for alloys? Let’s find out!
Recommended Video for you:
Can Alloys Be Separated Into Their Base Metals?
Unlike ores (naturally occurring) and other unrefined mixtures, alloys are an intended culmination of various metals in fixed ratios. Some of the common alloys with their constituent elements are listed below:
1. Brass (copper and zinc)
2. Bronze (copper and tin)
3. Solder (tin and lead)
4. Sterling silver (silver and copper)
5. Steel (iron, carbon, nickel, chromium, manganese etc.)
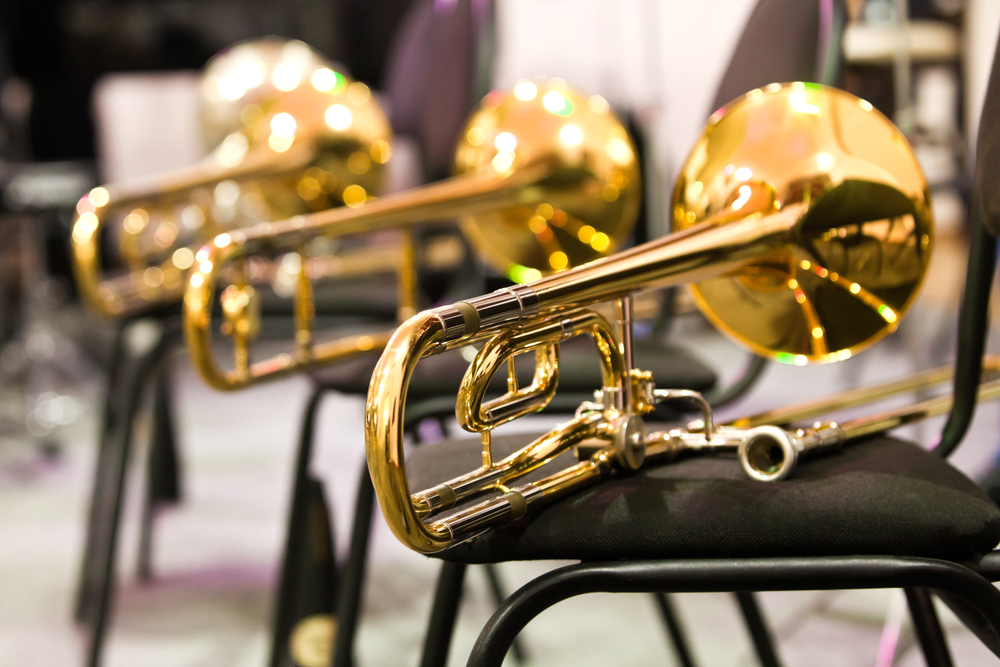
Reversing an alloy to its constituting elements is possible with various techniques. However, the result may not be distinctly separated metals, but rather a concentrated mixture of them.
What Are The Various Methods To Separate Alloys Into Their Base Metals?
Alloys can be segregated into their constituting elements using various techniques designed around differences in the physical and chemical properties of the material.
1. Liquation Of Alloys
Liquation is one of the most basic methods for separating alloys into their base metals. It relies on the difference in melting points of the constituting metals. Therefore, it is preferable for metals with large differences in their melting points.
Liquation is one of the most traditional methods of purifying metals from their alloys. (Gif Credit : Tutorvista.com)
Traditionally carried out in a furnace, liquation is useful for purposes of metal extraction from alloys and ore refining. Commonly refined metals include lead, tin, bismuth and zinc. This method is particularly beneficial in silver-tin alloys, where tin melts and flows out, while silver crystallizes and is readily separated.
2. Electrolysis Of Alloys
Electrolysis is a chemical process in which the alloy is dissolved in an appropriate solvent and subjected to an electric current. This causes the desired metals to deposit on the cathode, with impurities on the anode, or in suspension in the electrolyte itself.
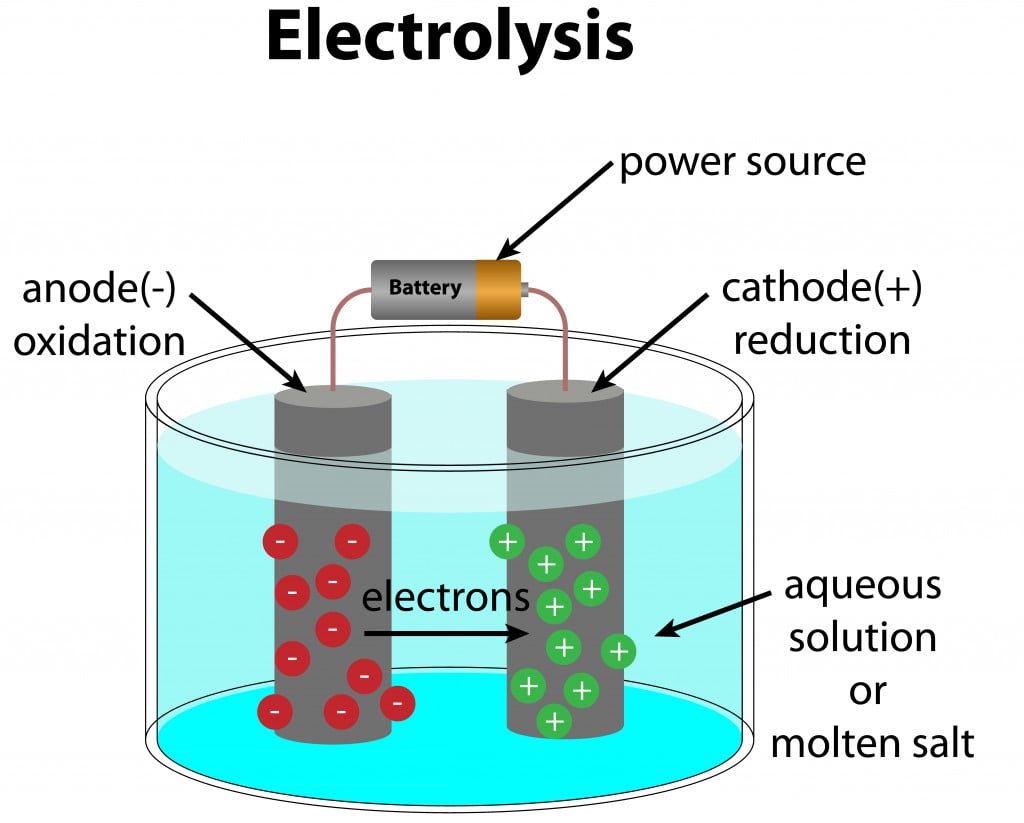
However, electrolysis is a complicated process, as it can be difficult to find the right solvent for the alloys in question. Electrolysis is based on reduction potential, i.e., the ability to gain electrons. Therefore, it is best suited for alloys whose constituting elements have a large difference in their reduction potential.
Common examples of metals refined using electrolysis include gold-silver, platinum-palladium, copper-zinc, nickel-cobalt, and lead-antimony.
3. Smelting
Smelting is used for extracting metals from their ores, in either their elemental state or as a compound. Ores are not necessarily metal alloys. Thus, smelting cannot be strictly categorized as an alloy separation technique. It involves heating the ore or compound in the presence of an agent that promotes reduction (loss of oxide components of a metallic compound). This reducing agent typically contains carbon, which combines with oxygen to form carbon dioxide.
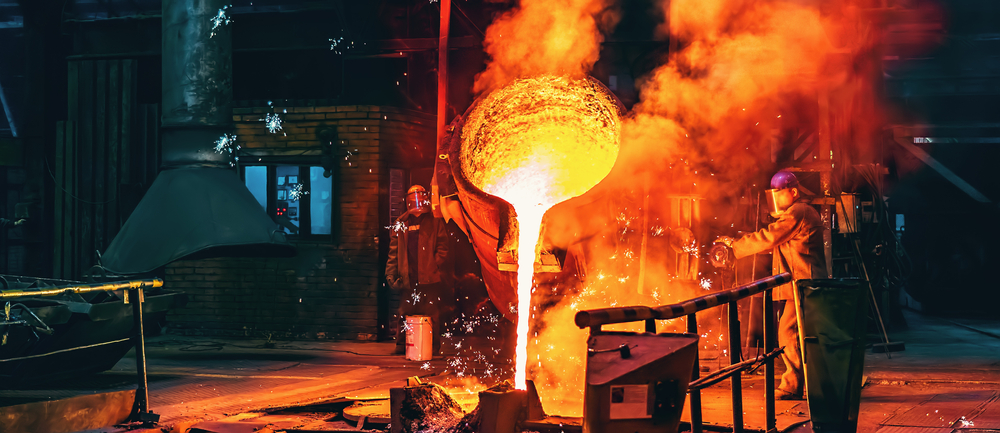
Interestingly, reduction promoter isn’t the only refining agent used in smelting. Metallurgists frequently make use of fluxes that bring about the formation of slag—a slurry of compounds of unwanted materials in an ore. Iron is the most commonly extracted metal that uses the smelting technique.
4. Leaching
The process of leaching relies on a metal’s chemical characteristics that differentiate it from the other metals in an alloy. Leaching involves reacting an alloy with a solvent, usually an acid or a cyanide solution, to dissolve a particular metal in the alloy. The result can either yield a pure metal, or a metal compound, which can then be further refined using other techniques.
Leaching is useful for the extraction of precious metals like gold and silver. It is also useful for extracting uranium from Brannerite, an ore that also includes titanium.
5. Solvent Extraction
Sometimes, it can become extremely difficult to separate metals from their alloys using traditional methods. In such cases, solvent extraction presents a viable solution.
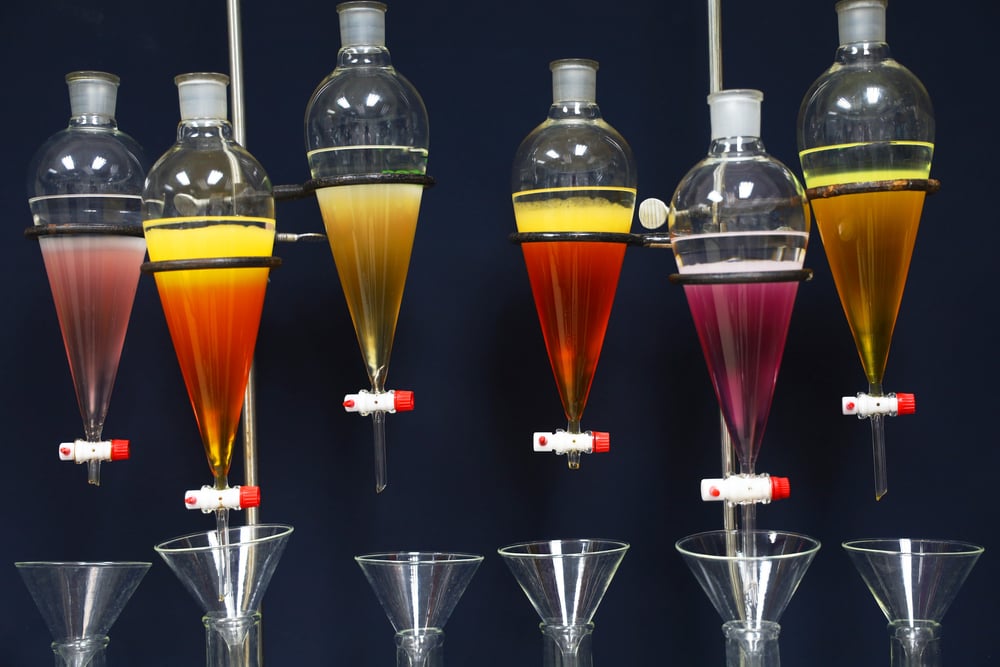
Solvent extraction bases itself on the selective solubility of metals in a given solvent. When an alloy is introduced into the solvent, one of the metals dissolves, while the other can precipitate in its pure state or as a compound. The precipitate can be refined further to obtain a purer state of the metal.
Examples of metals that can be extracted by solvent extraction include cobalt, uranium, nickel, copper and several rare earth metals.
Feasibility Of Separating Alloys Into Their Base Metals
While it is possible to separate alloys into their base metals, it is not necessarily economical to do so. Unlike ores, separating alloy mixtures cannot be seen as a scalable source for obtaining metals.
That said, there are some uses of alloy separation:
1. Testing The Purity Of Jewellery
Pure gold and platinum are soluble in aqua regia, a mixture of 1 parts concentrated nitric acid and 3 parts concentrated hydrochloric acid.
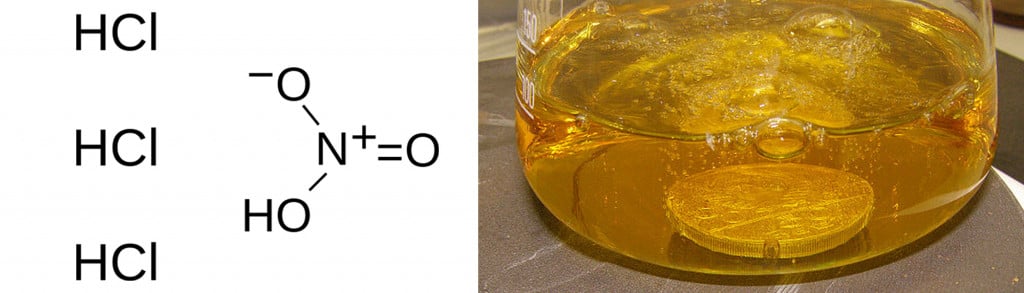
On the other hand, ‘impurities’ like silver and iridium do not dissolve in it. This can be used to test pieces of jewelry for the presence of cheaper materials.
2. Pollution Control
Industrial effluents often contain metals in toxic quantities and combinations. If let into common dumping grounds like landfills and seawater, they can wreak havoc on their surrounding ecosystem (source).
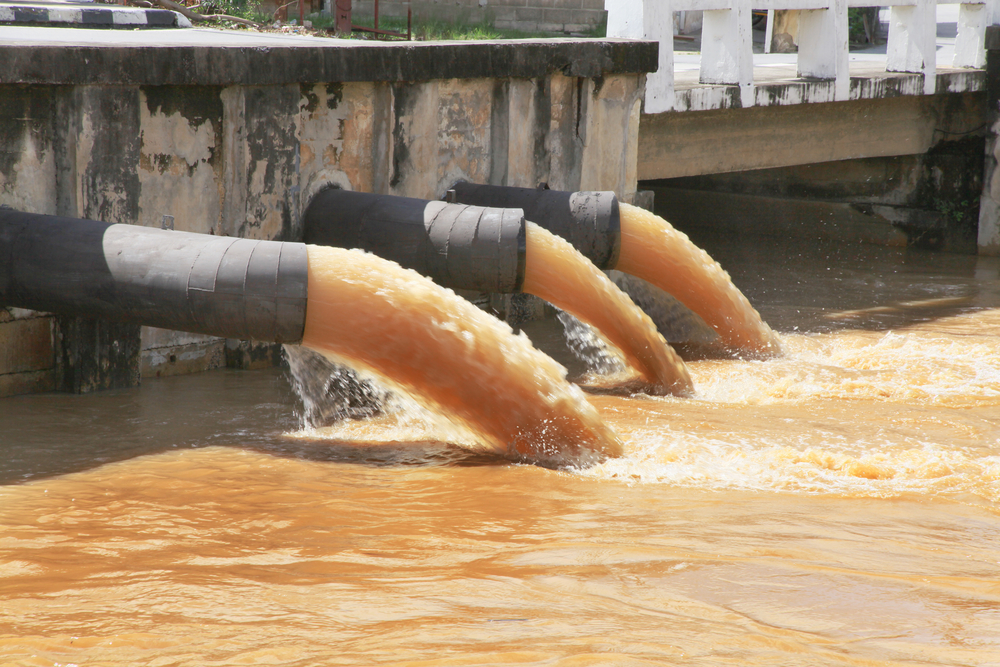
Thus, isolating these metals is an important part of effluent treatment prior to discharge into the environment. Heavy metals like lead, cadmium and mercury are common examples of such metals.
3. Recycling
Recycling scrap is one of the biggest applications of segregating base metals from their alloys. Sometimes, precious metals or their oxides are used in various machine components, and must be separated out carefully.
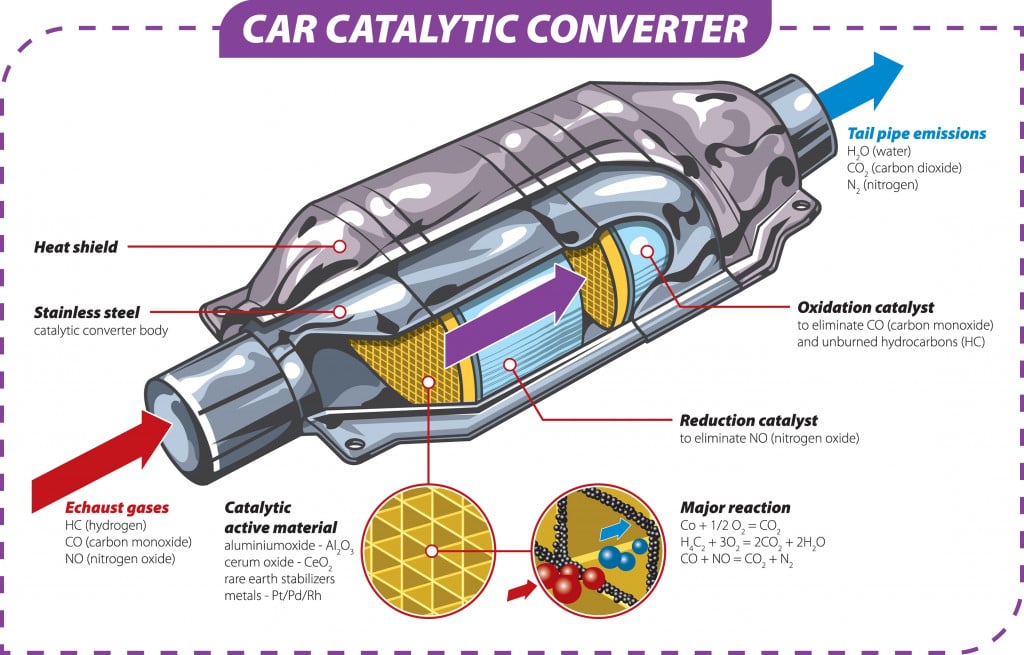
They are recovered before the out-of-spec components are scrapped and reused. Platinum, used in the catalytic converters of internal combustion engines, is an important example of metal that can be recovered from its alloys.
A Final Word
Often, no single process can be looked at as a complete solution for extracting metals from their alloys. Usually, one process refines the alloys to a concentrated mixture of the desired metals or their compounds. They are usually supplemented by another process to extract these metals from their compound state.
Overall, the value of the alloy, in most cases, is more than the sum total of its constituting metals, which makes their recovery an unprofitable endeavor.
References (click to expand)
- Recycling of metals from waste Sn-based alloys by vacuum .... ysxbcn.com
- Chen, Y., & Yang, H. (2019, April). Separation of Antimony from Copper in Vacuum Distillation. In IOP Conference Series: Earth and Environmental Science (Vol. 252, No. 2, p. 022035). IOP Publishing.
- Recycling of Automotive Wrought Alloys. books-library.net
- Uranium Mining and Extraction from Ore - Stanford University. Stanford University
- In Situ Leach Mining of Uranium - World Nuclear Association. World Nuclear Association